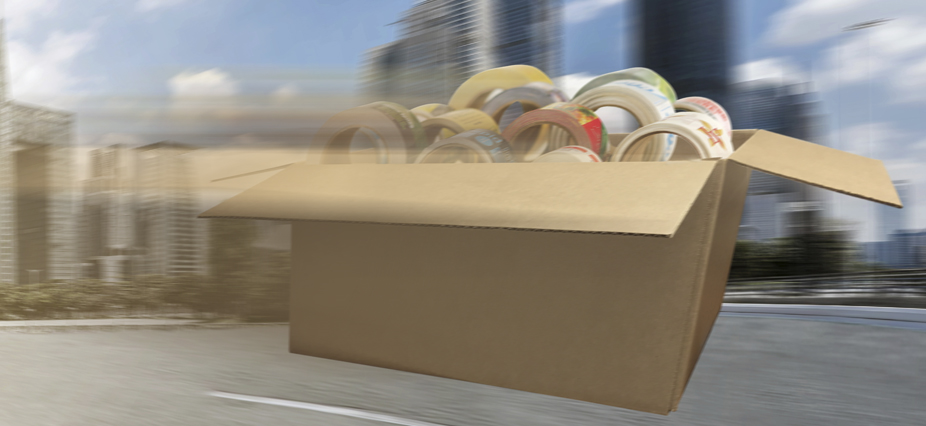
Why Worry About Expediting
While it may seem like a simple question, the answer has a much larger impact than what you might expect. We pride ourselves on getting our product to you, the customer, as fast as possible! In doing so, you can get your product on the shelf, display your brand or spread your message, faster. That sounds like a win-win for everyone!
Whenever the proper steps are taken to ensure an order is set up to be expedited, time down the road is saved, such as not having to worry about revisions. We all know the saying, ‘Time Is Money,’ and this applies to our customers. The longer we wait to get your label perfected, the longer you wait to get the label into action. Whenever we both have the same goal in mind, the result is going to be great!
Six Key Questions for Placing an Order
Our team of experts is always here to help with every step of the way, but keeping these six questions in mind will help you to create the best label and receive it in a timely fashion. By simply answering these questions, you will be on your way to placing an order in no time!
1. What will the size and quantity be?
With die-cut shapes ranging from circles, ovals and seals to rectangles or special shapes, knowing the shape and size you want your label to be is the first step in the process. Maybe our die-cut labels aren’t right for you – No worries! Our AnyShape® Labels can be cut to any shape or contour that you require. Don’t forget to think about quantity, too. From smaller orders to larger quantities, we’re ready to get the job done either way. Need 15,000 or more labels? Ask a sales associate for a quote for further information!
2. What is the paper stock and ink color?
Thinking about your paper stock is vital to determining the overall look of your label. With tons of options to choose from in our catalog, it can be hard to narrow down which is best for your label. Luckily, our Order Processing department can come to the rescue! “[Order Processing] is the main force who deals with incoming customers calling for quotes and reorders,” said Order Processer Alyxandria Sallee. “We can definitely assist with product knowledge on what would be the best fit for their particular job. We can also send out samples of the stock for customers to test out themselves.”
When thinking about ink colors, we offer our standard colors and more colors that can be added for an additional charge. We can also custom match a color for a fee per color.
3. What will the label be applied to? Different surfaces may require certain paper stocks or adhesive options. Some labels require different adhesive placements, such as on the face or back of the label. Others might require an opaque adhesive used to cover up copy from showing through the face stock. Further on in this article, we will look at our Stock & Adhesive Guide that will help you to select the perfect combination.
4. What will the label be exposed to?
Water, solvents, dust, outdoor elements and other factors all play into the life of a label, as well as the materials the label is made of. When looking into a product that lasts, try our Extended Life Durable Decals that can withstand harsh conditions for up to 4 years or our Weatherproof Labels that can withstand normal weather conditions for up to 1 ½ years.
5. Will the label be hand or machine applied? Thinking about core size, roll quantity and rewind direction are all vital to the application of your label. Whether they are being applied by hand or by a machine, these are still important things to consider. Machines that apply labels have requirements that must be met to ensure a proper application. Verify your machine’s requirements before placing the order to confirm that your core size, rewind direction and maximum roll size are all correct.
6. Is custom finishing or packaging required? Customers sometimes request special packaging or shipping instructions, and we do our best to accommodate their needs for a particular job. Some customers will request their orders to be shrink-wrapped or divided into stacks of a set quantity to make it easier for distribution. This can also make it easier for the customer to count, keep track or store. Additionally, customers might ask for their labels to be perforated which allows them to quickly be torn off. For example, a school might request labels that are perforated for an open house event so that they can easily hand them out as students and families come in.
Remember the Six Questions
Applying these questions to your order can help to get you started and having a good idea of what you want from your label will help to speed up the process. If there are further questions, our Order Processing team is always here to help @ 800.995.9500.